|
|
|
|
|
|
|
|
|
|
|
|
|
|
|
|
 |
|
|
|
|
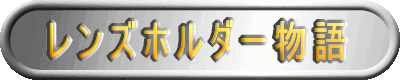 |
|
|
|
|
 |
|
|
|
|
|
|
|
|
|
|
|
|
|
|
|
|
 |
|
|
|
我々が試作開発を始める1年ほど前に、西ドイツにカップ状のダイヤモンドホイ−ルと言うもので、平面からどんな球面でも削ることの出来る機械が有るとの情報を得て研究を始め、その後ダマ社のカ−ブゼネレ−タ−の見学をする機会があり、これを参考に1951年に国産1号機のカ−ブゼネレ−タ−の機械部分の試作が出来上がったのですが、当時2極(ツ−ポ−ル)モ−タ−が日立、東芝等のモ−タ−メ−カ−で製作をしていなく、ボ−ル盤メ−カ−の並木製作所の方々が熱心に考えて作って頂きました。
ダイヤ軸を10000回転位にしたかったのですが、国内にはそれに対応できるベアリングが無く、スェ−デン製のテ−パ−ロ−ラ−ベアリングを使用して7000回転としました。
ダイヤモンドホイ−ルも無く、帝国光学さんより西ドイツ製ホイ−ルを借り受けて、東京ダイヤさんに持ち込んだのですが、こんなものは見たことが無いと首をかしげるばかりでしたが、とにかく割って中を見ても良いからとお願いをしてやっと出来上がり、これが日本で初めて光学ガラスに国産のダイヤモンドの研削機械、工具が取り入れられた始まりで、レンズ研磨の第一工程(荒摺り)が大幅に合理化されることになりました。
この国産1号機は、顕微鏡メ−カ−のクリヤ精光さんに納入させて頂きました。
レンズの切削の為に、ダイヤ軸の中心から切削液を出したところ、一日中使用してると切削液がベルト側に戻り、ベルトが駄目になる事がわかり困っていたところ、クリヤ精光の社長さんが考えてダイヤホイールの螺子の際に孔を開けたらとの提案で、切削液の逆流は無くなり現在も利用しております。
この時にレンズをチャツクする物の材質形状も種々試作、研削した結果、ガラスに傷をつけない材質としてベ−クライト、形状は現在も使用されている型となり、これにより片肉・中心肉厚とも外径のバラツキにかかわらず、
±2/100mm以内に研削が出来るようになりました。
当時、荒摺りは手での作業でしたのでレンズの外形は指定寸法に対して±0.6以上ありましたが、ゼネレ−タ−の普及により大分寸法のバラツキが少なくなってきましたし、当時のレンズ職人の方々は手の指先の爪は摺り減って殆ど無い状態でした。
1960年頃に、アメリカよりス−パ−カットの名称で当社にもダイヤモンドペレットの売り込みが何度かあり、1粒が当時の価格で2ドル720円と非常に高く使える状態ではなかったのですが、近い将来に国内でも製作使用の時が来る予感は致しました。
又、その頃からレンズ研磨の高速化が要求されるようになり、カンザシ運動が擬似楕円運動の高速合型HL4−Vを製作しました。
この機械の大きな特徴は、上皿がオスカ−振りのように振り幅の左右両端で発生する遠心力を極端に少なくする事が出来、またカンザシ加圧を重り式から新設計のスプリング加圧式としました。
これによりカンザシの運動を速くする事が可能となり、ニュートン面の安定も可能となりました。
カンザシア−ムの上げ下げも軽く作業性も良くなりました。
同時に研磨剤の循環式の自動供給装置を開発し、擬似楕円運動、スプリングによるカンザシの加圧方式、研磨剤を各レンズ軸に供給を止めても、研磨剤は最良の状態で絶えず循環をしている自動供給方式の3点は、パテントを取得致しました。
当時、研磨剤のかけ流しをしていたのでは、良好なレンズは磨けないという人もいましたが、我々は研磨剤は研磨と冷却を兼ねているとの理論を現在も持ち続けており、この研磨剤供給方式は世界各地で利用されております。
国内で初の量産型高速研磨機として国内、海外に相当数を製作納品を致しました。
これの改良型は、現在でも多数の生産をして各レンズメ−カ−さんに納入をしております。
このHL4−Vの研磨機は大阪の造幣局へ納入をしており、その時にコインについていろいろと知りました。
コインの外径は必ずふちが有りますが、両面に刻印した時に平面を保つために必要なのです。
海外から造幣局へ研修に来た数か国の人達のご指名で、海外の造幣局にも納入使用されております。
1969年(昭和44年)に、三和精密工業株式会社さんがダイヤモンドペレットを開発し製造、発売をしましたがダイヤペレットが必要とする切削速度のある研削機械が無く、販売に大変苦労をしているようでした。
その後、当社に相談があり、それと前後してフランスのCMV社がレンズホルダ−による研磨方式を開発したとの話を聞き、また見る機会も有りましたが、イメ−ジとしては光学レンズの研磨には向かないと判断を致しましたが、参考にはなりました。
さらに前後して、西ドイツからリセス皿による高速研磨方式が入ってきて、大手のメ−カ−さんの採用が相次ぎました。
私の検討の結果、従来より
@高精度の皿が必要
A皿に精度の良い座ぐりの出来る機械が必要
Bどのくらいの生産数か予測が必要
C大型のカ−ブゼネレ−タ−が必要
Dレンズの面取りが出来ない為、面取りのされたレンズの研磨よりパット皿
の摩耗が早い
E脂貼り剥がしが必要
F脂の洗浄が必要
等、との問題が有り(昭和42年)に開発発売をした小型高速研磨機、Bタイプでベ−ク樹脂製のレンズホルダ−による1個研磨の方式は、レンズの脂貼り、剥がし、が無く再研磨、肉厚測定が直ぐに出来る、のメリットを最大限生かすべくホルダ−の形状等の研究に入り、最初はカンザシ先端とレンズホルダ−の中心のカンザシ受けに鋼の焼き入れ品を使用したのですが、耐久性で問題外となり高価ではあったのですが、初めて超硬チップ付きカンザシを取り入れ、試研磨の結果ある目的の為、先端の曲がりを5°15°30°の物を作りました。
これと並行して、ダイヤモンドペレット皿でのラフポリッシングの研削実験を開始しました。
ペレット皿の回転速度を上げ、切削速度を得る為とニュ−トン面の安定を図る為、原則としてレンズ直径の倍径の皿を使用する事と「皿は下」「レンズは上」で研削、研磨をする事としました。
これは、研磨皿の面変化を少なくする事とレンズの着脱時間を短くする為で、現在1個研磨はこの方式が主流となっております。
タイマ−により停止時間を決め、最初は♯1200のダイヤモンドペレット皿を使用、切削加圧はエア−シリンダ−として皿軸回転数を通常砂掛け研磨機としては、速い回転数と言われている300回転で研削実験を始めたのですが、考えられないような大きな傷が入りましたので、1000回転にしたところレンズ面の傷は少なくなりましたが、皿軸回転の停止時のエナ−シャが有り、又高速回転で研削をしても、停止時の0回転迄エア−シリンダ−の加圧がそのままですので、結果はあまり良くなかったので皿軸回転を2000回転にしてブレ−キモ−タ−を取り付け、エア−シリンダ−の加圧もモ−タ−回転と同時に加圧が入り、タイムアップと同時にブレ−キモ−タ−停止と、加圧が解除するシステムとして、ワンボタンプッシュ作動回路をつくり、作業性も格段と良くなり、ペレット疵は無くなると同時に砂の♯2000くらいの粗さに仕上がりました。
研磨機にも、ワンボタンプッシュシステムを取り付けました。
このシステムは、スタ−トボタンを1回押すだけで済み、現在多くの会社がこのシステムを利用しております。
この結果、研削時間が20秒以内で良好な面に仕上がり、砂掛け作業の環境が大変良くなりました。
しかし、ブレ−キモ−タ−のブレ−キが放熱出来ず、焼きついてしまう問題が発生したので、日立製作所さんにお願いをして、焼けない耐久性のあるブレ−キを開発をして頂きました。
当時、皿は使う人が基本Rの皿を購入後、荒摺機いわゆるダライ盤で砂摺りを行い、要求されるニュートンの本数になるように経験則でRを決めていました。
しかし、ダイヤペレット皿を使うとなると、砂摺りではダイヤが減らず無理なのと、レンズホルダーに依る1個研磨の場合、特にコバ肉の厚さが必要となり、それらの計算式を当時のコンピューター言語ベーシックを用いて、基本R、レンズ径、ニュートンの本数のデータで求めるRが計算できるソフトを作り、またレンズ径、上下のR、中心肉厚のデータでコバ肉が計算出来るソフト、カーブゼネレーターのダイヤ径とRのデーター入力で、角度が求められるソフト等を作り、ゼネの角度は誰でも解る円形座標を作り、一般に公開し、同業者にも業界の品質向上の為と思い指導もしましたが、同業者の中には自分で開発したが如くに言い「ニュートンの本数さえ言ってくれれば求めるR皿を納めます」などと宣伝している者もおりますが、品質がよくないのが現状です。
R皿はNC旋盤のようなデジタルの機械では完全なRは出来ませんし、レンズ研磨と同様にアナログの機械でないと完全なRの皿は出来ません。
しかし、当時はこの様な研磨方法、特に凸レンズを上で磨く事、レンズホルダ−にレンズを接着せず外径に緩みの有る装着方法は、研磨の職人と言われる方々から「こんな方法ではニユ−トンが出ないよ」と言われました。
自分では自信のある研磨方法と思ったのですが、約2年間はカメラ関係の光学界では採用されませんでした。
仕方がなく眼鏡関係に売り込みをはかり、一部採用されましたが脂貼りピッチ研磨でなくては駄目と断られる会社が多数でした。
双眼鏡業界でも同じようでした。
同じ双眼鏡業界でも、香港のハッキング社とコンタクトを取りましたら、直ぐに採用されカ−ブゼネレ−タ−、ペレット機、小型高速研磨機のラインを相当数購入して頂き、レンズの生産数が飛躍的に増えコストダウンが大きいと喜ばれました。
当時、ハッキング社は日本の双眼鏡業界の人々に自由に社内見学をさせていましたので、宇田川のシステムを見て何で香港に売ったのだと、わざわざ私のところに業界の上層部の人がクレ−ムの電話を掛けてきた事もありました。
私としては、カメラ業界に採用を願って開発をした結果で大きな挫折感を味わいましたが、低価格、簡単な操作という事で各カメラメ−カ−に売り込みを図ったのですが駄目でした。
ある時、甲府コニカの関さん(コニカ大連総経理後退社)がいらっしゃつてこのシステムをご覧になって「宇田川さん、この方法でレンズは磨けるよ」と言われ生涯忘れる事の出来ない大きな喜びでした。
その上、カメラ業界で初めてこのシステムを採用して頂きました。
その後、コニカさんが採用したとの話が外部に伝わり、中堅のカメラレンズメ−カ−さんが、続々と採用する様になりました。
現在、宇田川鐵工が開発したレンズホルダーによる1個研磨方式は、低価格、高品質、高精度なレンズ加工が出来るとして、各国のレンズメーカーが採用をしておりレンズホルダー無しでは、レンズの研磨は考えられないところまできております。
それと前後して、従来コパ肉の無いレンズは皿に脂貼りとなり、当然変心等が有りダイヤモンドペレットの切削必要速度まで回転を上げて研削する事が出来ず、そこで従来無かったカンザシを下皿に対して逆回転させる方法で上皿を回転させ、周速の差を少なくする為に上軸は前後揺動、下軸は適度に前傾斜させる事により、ダイヤの切削速度を得ると同時にニュートン面の安定もよく、中型と大型の機種を作り現在も多数生産をしております。
その後凸面レンズの磨きにくいものが出て来ました。
当時、ドイツのロ−社から上のカンザシ軸が球芯揺動の機械が、入って来ました。
弊社でも、カンザシ軸の球芯揺動方式と下皿軸が球芯揺動方式の二機種を作り研磨実験を行った結果、R面の芯振れ精度、Rの中心と機械の揺動中心とが一致させなければならず、又研磨範囲が限定され、機械本体の価格も高くなりランニングコストも高く付く、との結果から平面から半球越え迄磨ける機械として下皿軸を垂直から30度迄任意の角度に前傾斜をさせ、上のカンザシ軸を前後揺動する機械を開発しました。
現在は、皿軸を垂直から60°まで任意の角度を前傾斜させられる機械も開発してあります。
この運動の組み合わせで、球芯揺動に近いカンザシ加圧が得られます。
小径のレンズから平面まで磨ける研磨機として、各レンズメ−カ−さんに多数ご利用頂いております。
顕微鏡の対物レンズの砂掛け研磨用として、カンザシ部が完全円運動で下軸が垂直から30°まで任意の角度に設定出来る高速研磨機を、開発ユ−ザ−に喜ばれております。
この頃から、パテントを種々の事情から取得しないようにしました。
例えば、パテントの申請をしても種々の理屈を並べて拒絶をしてきます。
反論書を提出すると間違えなく、この様な考案は誰でも考えられるもので特許に値しない、との拒絶書が返ってきますが、それならば最初から誰でもこんなアイデアは考えられるもので特許に値しないと拒絶をすればいいものをと思いますが、これでパテントの出願は終わりと思い拒絶された後、審判に持ち込みパテントを取りました。
中型多数貼りペレット機のパテントの申請をして拒絶されましたが、約10年後に某大手メーカーが全く同じものを作りパテントの申請をしました。
申請内容の文章は、機械が同じですので殆ど同じでしたがパテントが取れたのには驚きました.
その後は、同業者と争うのは嫌なのでパテントは取らずにいます。
良い機械には、必ず同業他社のコピ−品が出ると我々は思っていましたが、各種機械にコピ−品が多数出廻っており、精度が悪く問題を起こしているメ−カ−もあります。
コピ−品が出るという事は我々の機械が評価されていると考えております。
現在、国内で作られている光学用機械の70〜80%は、弊社のコピーを取り入れた機械です。
約20年前くらいに、柔らかく粘りのあるSF系統のガラスが出てきて、研磨は低速、低圧でないと磨くことが出来ないと苦労をしているのをみて、最初は機械の回転を「低速」「高速」「低速」とタイマーでプログラムを組んでテストを行い結果は良かったのですが、機械の構造上うまくないのでエアー加圧で「低圧」「高圧」「低圧」の3段加圧をタイマーでプログラムを組みテストを行ったところ、結果が良く特定の各研磨会社に機械の納入をして現在に至っております。
納入先の工場によって「高圧」「低圧」の2段加圧方式で納入しています。
エアーレギュレーターの調整で、加圧はどの様にでもなります。
最近、他社でこの方式を自社のカタログに掲載している会社もあります。
コンピューター付きの研磨機も有りますが、どんな高性能のコンピューターを用いても、平面の研磨皿で高精度の球面のレンズは絶対に磨けません。
レンズ研磨は、ある意味では印刷と同じで高性能のレンズを磨き上げるのには高精度の研磨皿が必要です。
研磨皿をコンピュータ付きの機械で作れるのならば、研磨の革命になるのではないかと思いますが、それは無理でしょう。
経験の豊かな研磨技術者と高精度の研磨皿と、それに対応する研磨機が無ければ精度の高いレンズは絶対に作れません。
海外に研磨技術が流出してしまった今日、これからは高精度、超寿命、トータルコストの安い機械でないと、海外製品に太刀打ちが出来ないと思います。
宇田川鐵工は、国内で入手できる最高品質の品物を金額にかかわらず絶えず求めております。
他社のように10年、15年でアフターサービスを打ち切ることも無く、現在でも40年以上前の研磨機械を使っており、ユーザーはいつでもアフターサービスを受けられると安心しております。
京セラさんから、膝、腰等のジョイント部に使用するセラミックス製の人工骨の素材を持って来られ、商品化をしたいので研磨装置と研磨方法を開発して欲しいとの要望が有り、以前に商品化した上下皿の逆回転の機械を下皿軸を60度傾斜させ砂で中間仕上げをしたあと、酸化セリュウムで24時間研磨をしましたが全く変化がありませんでした。
その時に、セラミックスの硬さを思い知らされました。仕方がなく当時月給1か月分の高価なアメリカ製のダイヤモンドパウダ−を購入して研磨をしたところ、10分位で完全な鏡面になりセラミックスメ−カ−さんに喜ばれ機械を購入して頂きました。
オリンパスさんから、胃カメラ用のファイバ−端面の研磨装置の依頼を受け試作実験をしながら、これからは体の中を切らずに診察が出来る時代が来るんだとの想いがありました。
ファックスも各社から種々と相談を受け、近い将来電話で声以外に文字、絵等が送れる時が来る、レ−ザ−ディスクの光読み取りレンズについて相談を受けレコ−ド盤状の物で音と絵が同時に出る装置が出来る等、日本ではじめての試作に関わる事が出来ました。
クォーツ時計を開発、それに使用するクォーツの大量研磨の方法の相談を受け、当時の歯車式時計は1日1〜2分の狂いは当たり前な時に、1ヶ月20秒以内ですとの話に大変驚き、亦量産しても30万位と言われて一生持てない時計かなとも思いました。
その他、あるメーカーさんから自動車の各種計器類は丸いガラスカバーで覆われた形状で、ダッシュボードに配置され目視の角度によっては見にくい場合があり、ガラスカバーを研磨して乱反射を除きたいとの相談を受けました。
今後、自動車の大量生産が始まると処理しきれなくなると思い、小生の経験則から計器類を一箇所に集め、全面を凹面状のカバーにすれば乱反射は非常に少なくなると思いますと話したところ、後日、良い結果が出ましたとの手紙を頂きました。
バックミラーの制作会社から、輸入米国車のルームミラーにプリズムミラーが取り付けられたのがあり、それを持参して「これと同じものを作りたいので機械があれば欲しい」との相談を受け、弊社製の平面ゼネレーターにプリズムミラーと同じ角度の治具皿を作り切削と研磨をしたところ、会社に帰り機械購入の予算を取りますから見積書が欲しいと言われ提出したところ、半月位して種々なデータを要求されそれらを出して、約1ヵ月後にある研磨機製作会社から機械を作らせて欲しいと懇願されたので、そこの会社に依頼することにしましたと1通の手紙で終わりにした会社もありました。
ある時、安全カミソリの刃について相談があり、当時の刃は刃先の部分の断面がV字型で肌に食い込みやすく肌が切れる場合もあり、また刃の寿命も短く何とかしたいとの事で、これも経験則で70Rか80Rのシリンドリカルの凹皿を作り、これで磨いてみてくださいと皿を提供したら、結果が良くパテントを取りたいとの話でしたので、どうぞと言ったところ非常に喜ばれました。
その他、現在も取引先からの依頼で未だ市場に出ていない商品の開発を数多く受けております。
例として、世界で初めて量産化に成功した、1個のレンズで360度見る事のできる監視カメラ用レンズ等です。
|
|
|
|
 |
|
|
|
|
|
|
|
|
|
|
|
|
|
|
|
|
 |
|
|
|
|
|
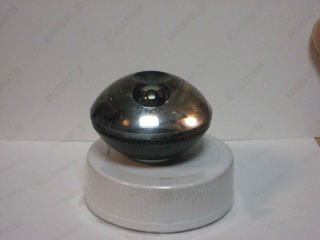 |
|
|
|
|
|
 |
|
|
|
|
|
|
|
|
|
|
|
|
|
|
|
|
 |
|
20年前の精度であるならば、現在のデジタル機器で作る事が可能でも現在の精度の物はやはりアナログの世界です。
研磨技術者の持っている技術は決して感(勘)ではなく、現在のコンピュタ−の能力ではソフト化出来ない高度で複雑な経験則の中にある技術です。
技術者が、仕事上から得られる経験則は最高の技術です。
レンズ研磨の世界は、研磨技術と機械の技術が半分ずつ持つと思います。
小生も多くの良き先輩と知り合い色々な技術、経験を頂き感謝の毎日ですが、既に多くの先輩がこの世を去り残念に思っております。
戦後の日本の光学界の裏側の一面を書き残したい気持ちで書きました。
1960年に社内製作品の完全規格化を行い、現在30年、40年以前の機械の消耗部品等を電話1本、FAX1枚で完全供給出来る事を弊社は誇りとしております。
|
|
 |
|
|
|
|
|
|
|
|
|
|
|
|
|
|
|
|
 |
|
|
■宇田川鐵工株式会社 社是
今日会う人は皆師なり
物作りは社会の為
今日一日を無事過ごせたことに感謝する
人に感謝されるような仕事をする
人に迷惑をかけないこと
人に教える教え方を三つ持とう
学歴は必要ないけれど学力は必要
人生は一生勉強
人生に夢を持って物作りに励む
物作りはすべての物に興味を持とう
失敗は明日の技術になるよう努力する |
|
■私の信条
此の地球上に何十億の人達が住んで
居ようと会えば、お早う、今日は、
左様なら、と親しく挨拶のできる人が
自分にとって何人いるか知るべきで
あり、その人達の数が自分の実世界
であり、その他の人達は残念ながら
路傍の人達です。高々年賀状の数が
それを教えてくれています。知り得た
人達には誠心誠意を持って付き合い、
人々から感謝されるように心がけ、
また嘘、騙し、裏切る等の行為は
絶対にしない。
|
 |
|
|
|
|
|
|
|
|
|
|
|
|
|
|
|
|
 |
|
|
|
|
|
|
|
|
|
|
2007年7月1日 宇田川 健次
|
|
|
 |
|
|
|
|
|
|
|
|
|
|
|
|
|
|
|
|
 |
|
|
|
|
|
|
トップへ |
|
|
|
|
|
|
|
 |
 |
 |
 |
 |
 |
 |
 |
 |
 |
 |
 |
 |
 |
 |
 |
 |
 |